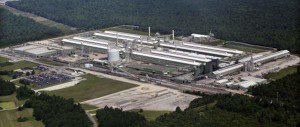
Via Press Release:
BERKELEY COUNTY, S.C.–About 600 employees at the Mt. Holly aluminum smelter in Goose Creek today received notices that Mt. Holly had been unable to reach agreement with Santee Cooper regarding transmission of energy to the smelter and, as a result, the plant will close at the end of 2015 unless Santee Cooper agrees to transmit the required energy.
In a letter to employees, Mt. Holly said that it had secured a power contract with a third-party provider to supply the required power at market rates. The third-party agreement would allow the plant to continue to operate if Santee Cooper would agree to deliver such power across Santee Cooper’s transmission lines.
Century Aluminum Spokesperson Samantha Dubay says the company has been unable to reach an agreement with Santee Cooper to do so, despite Mt. Holly’s offer to pay Santee Cooper the full transmission tariff rate – the same rate Santee Cooper charges other customers seeking similar service.
“Century acquired Mt. Holly because we believe in U. S. aluminum production, in the business environment in South Carolina, and in our employees,” the notice said. “Century wants to operate Mt. Holly in 2016, and for many years thereafter, but Mt. Holly cannot operate without competitively priced power.” Mt. Holly is the newest primary aluminum plant in the U.S. and the most efficient, except for an uncompetitive power contract with Santee Cooper that requires Mt. Holly to pay by far the highest power rate paid by any North American smelter.
“Between now and December 31 when the power contract expires, we will do everything we can to fight to get a new power contract that allows the plant to stay open,” the notice to employees said. “We will need your help in this fight.”
About 40 percent of a smelter’s cost of operations is power, which is far higher than other manufacturing companies.
Century Aluminum, owner of Mt. Holly, issued the conditional notice in compliance with the Worker Adjustment and Retraining Act, which requires notice to workers if the owner believes that a “mass layoff” will occur.
If the plant closes, the 600 employees will lose their jobs by December 31. The annual payroll is $50 million a year.
According to an economic analysis by Dr. Joey Von Nessen of the Darla Moore School of Business at the University of South Carolina:
- Holly’s direct economic impact on the Charleston tri-county region (Charleston, Berkeley and Dorchester) is $945 million a year.
- Holly’s direct and indirect job impact in the region is 2,058 jobs. The study found that the average income of these jobs is $60,000 a year, which is 48 percent higher than other manufacturing jobs across South Carolina. “For every 10 jobs created by the Mt. Holly facility, an additional 25 jobs are created elsewhere in the Charleston tri-county area,” according to the economic study.
- The impact of a shutdown would be felt across the state beyond the tri-county region. Statewide, the study says Mt. Holly has a $977 million impact on the economy and 2,300 jobs created, with $13.5 million in state taxes generated. About $135 million in labor income is produced, most of it in the Charleston region.
“These high-quality jobs are vital for the health of South Carolina’s economy, as they boost income levels and contribute to wage growth,” according to the study. “At the state level, every job created by Mt. Holly generates more than twice as many additional jobs for South Carolina as a job created in an average firm in South Carolina.”
The economic analysis concluded: “If the Mt. Holly facility were to exit South Carolina, then any in-state firm that uses aluminum or an aluminum product in its production process would ultimately reduce its in-state purchase activity by 12 percent. These ‘lost’ dollars would reduce the impact of each of these downstream firms. A Mt. Holly exit would also reduce the incentive for new firms that require aluminum as part of their production process to locate in South Carolina due to increased transportation costs associated with purchasing from out-of-state suppliers.”
Recent Comments